How to Implement Predictive Maintenance Using Machine Learning: A Step-by-Step Guide
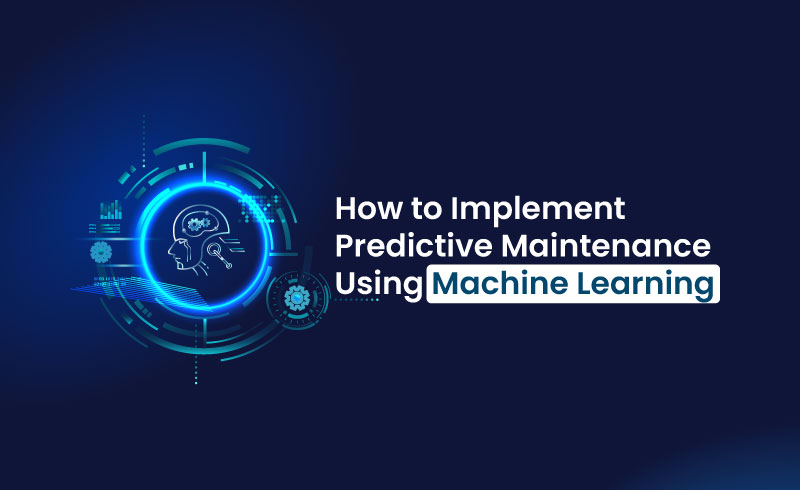
Predictive maintenance uses intelligent algorithms to predict how long machinery and components will last. Instead of sticking to a fixed maintenance schedule, this approach adapts based on actual usage, bringing several advantages:
- Better Maintenance Strategies: By foreseeing equipment failure, predictive maintenance tools enable timely actions, reducing unnecessary manual checks and minimizing downtime.
- Cost Savings: Real-time data analysis helps industries save on costs linked to unexpected outages and extended downtimes.
Machine learning plays a crucial role in making accurate failure predictions possible. It employs advanced models to analyze large amounts of data gathered from different sources, providing valuable insights into equipment health. Data analytics takes this further by handling and interpreting sensor data to anticipate potential breakdowns.
Implementing a strong predictive maintenance system is crucial for industries looking to cut downtime and operational expenses. You can hire web developers for analyzing predictive maintenance effectively. A well-executed system not only improves operational efficiency but also boosts overall business competitiveness in today’s digital era.
Understanding Predictive Maintenance
The Concept of Predictive Maintenance and Industry 4.0
Predicitive maintenance (PdM) uses data analytics and intelligent algorithms to predict equipment failures before they happen. This proactive approach is part of the broader Industry 4.0 movement, which focuses on integrating advanced technologies into industrial operations to create smart factories.
Industry 4.0 refers to the fourth industrial revolution characterized by the fusion of digital, physical, and biological systems through technologies such as IoT, big data, and AI in predictive maintenance . In this context, predictive maintenance plays a crucial role in enhancing maintenance management by enabling:
- Proactive fault prevention: Identifying potential issues before they lead to equipment failure.
- Optimized maintenance schedules: Aligning preditive maintenance activities with actual equipment conditions.
- Reduced downtime: Minimizing unplanned outages and production losses.
Differences Between Predictive Maintenance and Traditional Approaches
Reactive Maintenance
Reactive maintenance involves repairing or replacing equipment only after a failure has occurred. While this approach may seem cost-effective initially due to lower upfront costs, it often leads to:
- Increased downtime due to unexpected failures
- Higher repair costs from extensive damage
- Lower overall equipment effectiveness (OEE)
Example: A manufacturing plant that waits until a conveyor belt breaks down before fixing it may face prolonged production stoppages, resulting in significant financial losses.
Preventive Maintenance
Preventive maintenance (PM) schedules regular inspections and servicing based on predefined intervals or usage metrics. While more effective than reactive maintenance, PM can still be inefficient due to:
- Over-maintenance or under-maintenance risks
- Unnecessary labor and part replacement costs
- Limited adaptability to actual equipment conditions
Example: An automotive assembly line that replaces all machine parts every six months regardless of their condition might incur unnecessary expenses or miss critical wear signs that develop between scheduled inspections.
Predictive Maintenance
Predictive maintenance addresses the limitations of both reactive and preventive approaches by using real-time data and machine learning models to predict failures accurately. This allows for:
- Data-driven decisions on when to perform maintenance tasks.
- Extending the lifespan of machinery components.
- Reducing overall maintenance costs and improving efficiency.
Key Technological Enablers for Predictive Maintenance
Implementing an effective predictive maintenance AI strategy relies on several technological advancements:
Internet of Things (IoT)
IoT devices play a crucial role in collecting real-time data from various sensors embedded in machinery. These sensors monitor parameters such as temperature, vibration, pressure, and more.
Example: IoT-enabled sensors in an industrial robot can continuously track its operation metrics, providing valuable insights into its health and performance.
Big Data Analytics
The vast amount of data generated by IoT devices requires robust big data analytics platforms capable of processing and analyzing it efficiently. This helps identify patterns and trends that indicate potential failures.
Predictive maintenance Example: Analyzing historical sensor data from wind turbines can reveal specific operational conditions leading up to mechanical breakdowns.
Cloud Computing
Cloud computing offers scalable storage solutions and computational power necessary for handling large datasets generated by predictive maintenance systems. It also facilitates remote monitoring and analysis capabilities.
Example: A cloud-based predictive maintenance platform allows a global manufacturing company to centrally manage its equipment health across multiple facilities.
Machine Learning Techniques for Predictive Maintenance
Machine learning predictive analysis uses various machine learning methods to predict equipment failures and extend the lifespan of machinery. These methods can be grouped into three main categories:
Supervised Learning
Supervised learning relies on labeled datasets to train predictive models. Common supervised learning algorithms used in predictive maintenance include:
- Linear Regression: Predicts the remaining useful life (RUL) of equipment by finding the relationship between sensor data and equipment failure times.
- Decision Trees: Classifies data points based on historical failure patterns, making it easier to diagnose potential issues before they occur.
- Support Vector Machines (SVM): Uses hyperplanes to classify normal vs. abnormal operation states, aiding in early fault detection.
Example: In manufacturing, supervised learning can predict the wear and tear of machinery parts using historical sensor data, reducing unexpected downtimes.
Unsupervised Learning
Unsupervised learning does not require labeled data and is useful for anomaly detection:
- Clustering Algorithms: Techniques like K-means clustering group similar data points together, identifying anomalies as outliers.
- Principal Component Analysis (PCA): Reduces the dimensionality of sensor data, making it easier to detect unusual patterns that could indicate equipment failure.
Example: In an HVAC system, unsupervised learning can detect anomalies in temperature or pressure readings that might indicate a malfunction.
Deep Learning
Deep learning involves neural networks with multiple layers that can model complex relationships within vast datasets:
- Convolutional Neural Networks (CNNs): Effective for image-based diagnostics, such as detecting cracks or defects in machinery components.
- Recurrent Neural Networks (RNNs): Ideal for time-series analysis, RNNs can predict future equipment behavior based on historical performance data.
Example: Deep learning models can analyze vibration patterns from industrial motors to predict imminent failures more accurately than traditional methods.
Artificial Intelligence Complementing Machine Learning
Artificial intelligence (AI) enhances machine learning by enabling advanced predictive models:
- Expert Systems: AI-driven expert systems use domain knowledge to interpret machine learning outcomes and provide actionable insights.
- Reinforcement Learning: AI agents learn optimal maintenance strategies through trial and error, continuously improving upkeep schedules based on real-time feedback.
These AI applications ensure predictive maintenance using AI systems that are not only accurate but also adaptable to varying operational conditions.
Role of Data Analytics
Data analytics plays a crucial role in managing the vast amount of sensor data generated by industrial equipment:
- Data Cleaning and Preprocessing: Ensures the quality of input data by removing noise and handling missing values.
- Feature Engineering: Extracts relevant features from raw data, improving model accuracy and interpretability.
- Real-time Processing: Enables timely detection of anomalies by processing sensor data in real-time or near-real-time using technologies like Apache Kafka and Spark Streaming.
Example: In wind turbines, real-time data analytics can monitor blade vibrations and immediately alert operators to potential issues, preventing costly repairs.
Machine learning techniques such as supervised, unsupervised, and deep learning are the foundation of predictive maintenance strategies. By combining these techniques with AI capabilities and robust data analytics processes, industries can achieve highly accurate failure predictions and optimized maintenance schedules.
Steps to Implement a Successful Predictive Maintenance System with Machine Learning
Step-by-Step Guide to Implementation
Data Acquisition and Preprocessing
Implementing artificial intelligence in maintenance using machine learning begins with data acquisition and preprocessing. This stage is crucial, as the quality of your data directly impacts the accuracy of your predictive models.
- IoT Sensors: Utilize IoT sensors for real-time data collection. These sensors can monitor various parameters like temperature, vibration, and pressure. For instance, in a manufacturing plant, IoT sensors attached to machinery can continuously gather operational data.
- SCADA Systems: Supervisory Control and Data Acquisition (SCADA) systems can provide comprehensive data by collecting information from multiple sources across the facility. Integrating SCADA with IoT sensors ensures a richer dataset for analysis.
- Data Preprocessing: Clean and preprocess the collected data to remove noise and handle missing values. Techniques like normalization and feature scaling are essential to prepare the data for machine learning algorithms.
Conclusion
Using machine learning in predictive maintenance applications can greatly improve operational efficiency in your industry. By implementing strong predictive maintenance strategies, companies can shift from reactive or scheduled maintenance to a more proactive approach, resulting in less downtime and more optimized maintenance schedules.
Predictive maintenance goes beyond just preventing equipment failure; it also plays a significant role in business competitiveness during this era of digital transformation. By incorporating AI and data analytics into maintenance practices, businesses can stay ahead of the game by ensuring uninterrupted production and minimizing unexpected expenses.
Implementing these advanced methods not only brings immediate operational benefits but also prepares your company for future developments such as real-time streaming analytics and AI-driven decision-making systems. Investing in predictive maintenance today lays the foundation for sustainable growth and a competitive edge tomorrow.